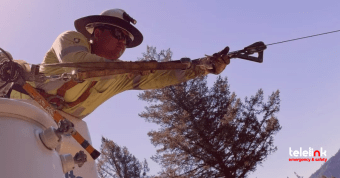
In the Oil & Gas industry, the practice of completing a trip risk assessment is common, especially for companies who utilize a Journey Management™ system.
In the utility industry, job briefings are commonly used to achieve a similar purpose; to review hazards associated with the job, among other procedural and work-related items.
There is, however, a small gap with some companies in the utility industry where workers leave for a job without completing a job brief and reviewing hazards — troublemen working on site alone. While requirements will vary from utility to utility, most troublemen do not conduct a job brief until they have to call in a crew to join them on site. Only then is a job brief carried out with a full review of hazards associated with the job.
Is there a safer way to dispatch troublemen and reduce their risk while working alone?
Photo credit: @thehungrylinehand
Trip risk assessment for troublemen
A trip risk assessment is a process outlining any potential hazards an employee may encounter while on a journey, but it is not only limited to ensuring that they get from point A to point B safely. All steps of the journey are considered, such as loading and unloading materials, getting into and exiting the vehicle, and ensuring the vehicle is properly maintained. When the steps are defined, a list of potential hazards is developed, with preventative measures to avoid them.
Considering that most call-outs occur during the evening and nighttime and when extreme weather causes damage, these sorts of hazard identifications and precautions become even more relevant for troublemen.
Modify for troublemen
Like any trip risk assessment, we can modify the template and ask questions that are more relevant for the utility at hand. Most importantly, we are able to establish a risk score and appropriate check-in time for the troubleman.
If we know the risk to be minimal, the check-in times can be spaced farther apart, however, if we know the risk level to be higher, more frequent check-ins will be required and the troubleman can communicate the risk to their 24/7 monitoring team.
Why GPS in the truck doesn’t suffice
Most, if not all service trucks have GPS tracking in them and it would be easy enough to think “if my truck has a GPS, then why do I need a personal device, too?” While you could have your trucks GPS tracked by a 24/7 monitoring team, the truck GPS is going to miss critical incidents such as:
- Man down: If a troubleman falls from a pole or any other considerable height they may be unconscious, seriously injured, and unable to make it back to the truck and communicate where they are or that they are hurt.
- No motion: Without a personal device, a troubleman knocked unconscious would have no way of notifying the monitoring team that something has happened. Electric shock, existing health issues, exhaustion, heatstroke, among others can cause a worker to slump and be motionless while unconscious. Fall detection may not catch the subtleties of these incidents but can save a brother from spending hours alone and unconscious in the bucket of a one-man service truck.
- Panic latch or panic button: The risk of physical attack is always present. If a troubleman is attacked, or at risk of attack, he or she may be unable to get back to the truck to give a distress signal and let the monitoring team know they need help.
Achieving the four key components of a lone worker solution
There are four minimum requirements for any decent lone worker procedure, all of which can be achieved using the trip risk assessment and a lone worker check-in solution. To keep the troublemen at your utility safer when responding to calls, consider implementing the following:
- Hazard assessment: Conduct hazard assessments and take measures to eliminate the hazard or minimize the risk from the hazard.
- 24/7 check-in: Establish a check-in procedure to ensure 24/7 contact is kept with all workers and a designated monitor is available.
- Two-way communication: Provide employees with two-way communication. If cellular phones are unreliable in particular areas, be sure to have alternative methods such as satellite technology.
- Location: It is important to know the location of the employee as close to real-time as possible. Where appropriate, use security measures such as surveillance cameras, rounded mirrors, GPS technology, etc.
How Telelink helps
Telelink does not manufacture its own lone worker devices and apps, instead, we take the role of unbiased advisor to help our clients find the best solution for their workers and associated risks. We know one size does not fit all because utility workers do not all face the same risks. We specialize in complex lone worker solutions and can offer our expertise and experience in crafting yours.
Telelink provides 24/7 monitoring for whatever technology solution you choose to monitor your lone workers with. Our dedicated safety team is trained to handle emergency situations with extreme precision. Visit our website to learn more or contact us today.
Post a Comment