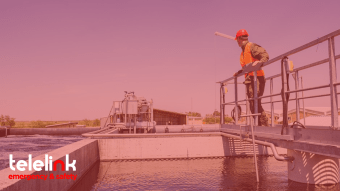
There has been a shift in lone worker safety procedures moving from manual systems to automated communication.
Traditionally, we have seen companies using a manual call-in system and periodic check-ins as a core part of their safety procedure. Even with advances in technology, check-ins remain important, functioning as the backbone of any Lone Worker safety program. Manual check-ins, however, provide very limited communication.
It's essential to understand that check-ins function as a fail-safe, alerting the company if a worker doesn't call in as scheduled. With each check-in the company is notified that a worker is either "okay" or "not okay" and nothing more. Because scheduled intervals are a part of the procedure, there's always a lag between check-ins. When a worker calls in once every four hours, the most current information the company has on hand is always out-dated.
There are many communication methods available in 2020. With advances in technology and connectivity, automation systems can improve a company's Lone Worker monitoring dramatically.
Automated monitoring check-in systems
Automated systems provide companies with real-time visibility and greater context around incoming communications from their workers. For example, if man down technology is employed for monitoring and emergency response, we can check in real time if an employee travelling down the highway is okay or not okay and whether or not we need to get to them right away. In the event that they require emergency response, their location is already known via GPS using this technology.
In emergency situations, when response times are critical, it's an advantage to use automated systems that are proactive not reactive. It's the difference between an agent getting the alert and responding in real time, or ahead of time, as opposed to after the fact.
Automation allows companies a lot of flexibility too. They can finesse their safety programs by setting up multiple alerts with different procedures for different units and regions. That way, if an employee hits the panic alarm on their app, or an in-vehicle monitoring system notifies us of a crash, those emergency situations will get a more immediate response than a worker calling in with a flat tire.
In-house monitoring vs. 3rd party monitoring
Traditionally, managers have monitored lone workers internally. Even though using an automated system has allowed managers to monitor their employees in real time, there's still a drawback to in-house monitoring. Simply put, the drawback is this: Managers have many other duties and responsibilities requiring their attention.
If a manager is responsible for monitoring lone workers in-house, it doesn't matter whether they are asleep at 3:00 a.m. or participating in a business meeting off-site at 3:00 p.m., they have to be prepared to respond swiftly to alerts. It isn't hard to imagine how something could slip through the cracks.
The fact of the matter is Legislation holds supervising individuals criminally responsible for Lone Worker safety. So it makes sense to reduce the burden on supervisory staff by employing third-party monitoring. Not only does a 3rd party monitoring solution like Telelink have a dedicated team in place that is ready to respond to alerts 24/7, this solution is often less expensive too.
Prescriptive Procedures vs. Risk-Based Programs
Traditionally, companies would apply one sweeping standard to all Lone Worker monitoring across all of their operations and all of their regions. This approach is cumbersome because it lumps all workers and all potential risks into one safety procedure. That is a prescriptive approach that doesn't allow much flexibility, and it often lacks a hazard assessment.
On the other hand, a risk-based program takes into account different job tasks, locations and communication risks. There's flexibility for different business groups and operating regions.
It may surprise you to hear that risk-based programs often result in a more simplified safety procedure that actually gets used more often by workers.
Post a Comment